
What is Ball Milling Process Dry Ball Milling Process
The ball milling process is generally divided into two types, the dry ball milling process, and the wet ball milling process. This article takes dry ball milling as an example to introduce Modelling of the HighEnergy Ball Milling Process,129 In this paper, the milling parameters of high energy ball mill (Fritsch Pulverisette 7) like vial geometry, number and size of balls and speed of the mill were modelled and Ball Milling method for synthesis of nanomaterials,1123 1. As the name suggests, the ball milling method consists of balls and a mill chamber. Therefore over all a ball mill contains a stainless steel container and many

Ball milling: a green technology for the
Ball milling is a simple, fast, costeffective green technology with enormous potential. One of the most interesting applications of this technology in the field of cellulose is the preparation and the chemical modification of Mechanistic Modeling of the Ball End Milling Process for ,200061 A mechanistic modeling approach to predicting cutting forces is developed for multiaxis ball end milling of freeform surfaces. The workpiece surface is represented by (PDF) A new conceptual model for ball milling,199311 several of the advanced models of ball mills, as well as other media mills (beinert et al., ), rely on collision energy information from simulations that do not include

(PDF) Grinding in Ball Mills: Modeling and
201261 The vibratory ball mill (VBM, Sweco, Belgium) consists of a 36 Lcapacity grinding chamber made of an abrasionresistant elastomer, put in vibrating motion by hightensile steel springs [28]..Prediction of ball milling performance by a convolutional ,51 A CNN model was developed to predict the ball mill process. • Training and testing datasets were generated from DEM simulations. • A threephase modelling Modelling and Control of Ball Mill Grinding,217 The universal structure of the model is an other advantage which gives access to the standard mathematical tools for process identification and control. Illustrations of this point are given by the
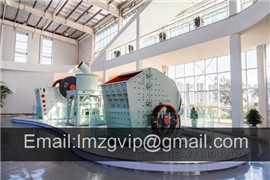
Modelling of the HighEnergy Ball Milling Process
120 In this paper, the milling parameters of high energy ball mill (Fritsch Pulverisette 7) like vial geometry, number and size of balls and speed of the mill were modelled and discussed. Simulations through discrete element method (DEM) provide correlation between the milling parameters. A mathematical model is used to improve and develop this process. The results Ball Milling Material Milling, Jet Milling AVEKA,Process What is Ball Milling? Ball milling is a size reduction technique that uses media in a rotating cylindrical chamber to mill materials to a fine powder. As the chamber rotates, the media is lifted up on the rising side and then cascades Modelling of the HighEnergy Ball Milling Process,In this paper, the milling parameters of high energy ball mill (Fritsch Pulverisette 7) like vial geometry, number and size of balls and speed of the mill were modelled and discussed. Simulations through discrete element method (DEM) provide correlation between the milling parameters. A mathematical model is used to improve and develop this process.
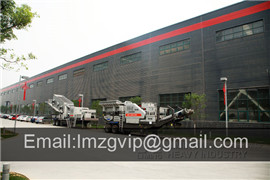
Mechanistic Modeling of the Ball End Milling Process for
200061 A mechanistic modeling approach to predicting cutting forces is developed for multiaxis ball end milling of freeform surfaces. The workpiece surface is represented by discretized point vectors. The modeling approach employs the cutting edge profile in either analytical or measured form.3D BallEnd Milling Force Model Using Instantaneous ,2005321 In this paper, we propose a mechanistic cutting force model for 3D ballend milling using instantaneous cutting force coefficients that are independent of the cutting conditions. The uncut chip thickness model for threedimensional machining considers cutter Ball milling: a green technology for the ,Ball milling is a simple, fast, costeffective green technology with enormous potential. One of the most interesting applications of this technology in the field of cellulose is the preparation and the chemical modification of cellulose

Heat generation model in the ballmilling process of a
21 A numerical model was then applied to calculate temperature distributions through the mill wall. Three possible combinations of heat transfer coefficients were analyzed, from (1) Kapakyulu and Moys, (2) Duda and (3) the heat transfer laboratory of Universitat Politècnica de Ball milling as an important pretreatment technique in ,812 Ball milling is typically the most effective and robust way of treating lignocellulosic biomass as not only the particle size is significantly reduced but also the crystallinity of cellulose and the degree of polymerization decrease [ 44, 45, 46 ]. Types of ball millsWhat is the Ball Milling in Mineral Process? Miningpedia,430 When the ball mill rotates, due to the friction between the grinding body and the inner wall of the ball mill, the grinding body is brought up in the direction of rotation and then falls down, and such materials are continuously pulverized. The grinding body has three motion states: falling type, centrifugal type and throwing type.
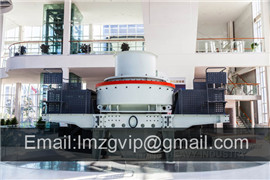
球磨机_百度百科
126 球磨机适用于粉磨各种矿石及其它物料,被广泛用于选矿,建材及化工等行业,可分为干式和湿式两种磨矿方式。 根据排矿方式不同,可分格子型和溢流型两种。 根据筒体形状可分为短筒球磨机、长筒球磨机、管磨机和圆锥型磨机四种。 [1] 工作原理 编辑 播报 球磨机是由水平的 筒体 ,进出料 空心轴 及磨头等部分组成,筒体为长的圆筒,筒内装有研磨体,筒体为钢板制 Ball milling as a synthesis method Aalto University Wiki,44 Ball milling process Ball milling is made possible by a cylindrical mill chamber and balls inside the chamber. These balls are usually very hard materials, like tungsten, silicon carbide, hardened steel etc. These small balls are made to rotate inside the chamber. Already powderous material will be made into nanosized material.Modelling of the HighEnergy Ball Milling Process,120 In this paper, the milling parameters of high energy ball mill (Fritsch Pulverisette 7) like vial geometry, number and size of balls and speed of the mill were modelled and discussed. Simulations through discrete element method (DEM) provide correlation between the milling parameters. A mathematical model is used to improve and develop this
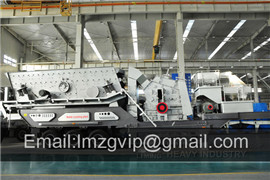
Modelling of the HighEnergy Ball Milling Process
The planetary ball mill process involves loading of the powders with the milling medium in a vial with severe deformation. The main parameters of planetary ball mill are [ 33 ]: Type of mill (mixer or planetary); Height and volume of vial; Operation: Milling duration, rotation speed, kinetic shock energy, shock frequency;Mechanistic Modeling of the Ball End Milling Process for ,200061 A mechanistic modeling approach to predicting cutting forces is developed for multiaxis ball end milling of freeform surfaces. The workpiece surface is represented by discretized point vectors. The modeling approach employs the cutting edge profile in either analytical or measured form.Ball Mill Application and Design Paul O. Abbe,Ball mills are simple in design, consisting of horizontal slow rotating vessels half filled with grinding media of ¼” to 1.5”. The particles to be milled are trapped between the grinding media or balls and are reduced in size by the actions of impact and attrition.
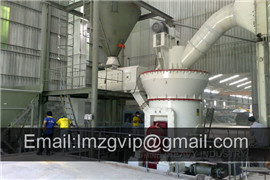
What is the Ball Milling in Mineral Process? Miningpedia
430 When the ball mill rotates, due to the friction between the grinding body and the inner wall of the ball mill, the grinding body is brought up in the direction of rotation and then falls down, and such materials are continuously pulverized. The grinding body has three motion states: falling type, centrifugal type and throwing type.Ball Mill Explained saVRee,There are three main stages to mineral processing in the mining industry. These are: Comminution (crushing and grinding). Beneficiation (separation and concentration). Smelting and refining. Ball mills are employed in the comminution stage as grinding machines ( Ball Milling The Role of Media and Bead Mills BYK,The ballmilling process uses a higher concentration of grinding media to mill base in which the chambers are designed to maximize the energy transfer. Bead Milling: The Dispermat SL model line When a particle size has to be reduced below 10 microns, bead milling is the technique to use.
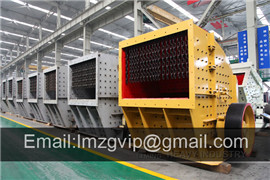
Process Control of Ball Mill Based on MPCDO Hindawi
726 In this paper, different from the traditional twoinputtwooutput model of the ball mill grinding process, a threeinputthreeoutput system considering the influence of three factors (i.e., fresh ore feed, dilution water, and mill feed water) is put forward to improve the accuracy of modeling.Ball Mills Mineral Processing & Metallurgy,213 SteelHead BallRod Mills are available in any one of five different types of discharge: Overflow, perforated overflow, return spiral, grate, and peripheral. To best serve your needs, the Trunnion can be ,
- الزاحف سحق تصنيع وحدة في مصر
- محجر البازلت الصخري ماليزيا
- German Stone Grinder Mill
- آلات الجبسي في اليمن
- كسارة الحجر الطلب المتوقع
- pclvertical shaft impact crusher
- التطبيقات الصناعية للكسارة الفكية
- نوع الكسارة في مصنع الأسمنت
- مطحنة الكرة رسم سقف أوتوكاد
- مصنعون لآلات تكسير الحجارة في مصر
- كسارة مخروطية تستخدم في الأشغال
- طحن الفحم في مصانع الاسمنت
- Break Up Blocker In Roughing Mill
- عملية إنتاج الذهب من الكوارت
- سعر كسارة تأثير الحجر الأملس
- limestone grinding machine cost
- معمل تكسير الجبس في العراق
- كسارة تشغيل الحجر الجيري لكل متر مربع
- small scale ball mills for sale and price
- صنع معمل الغسل في اليمن